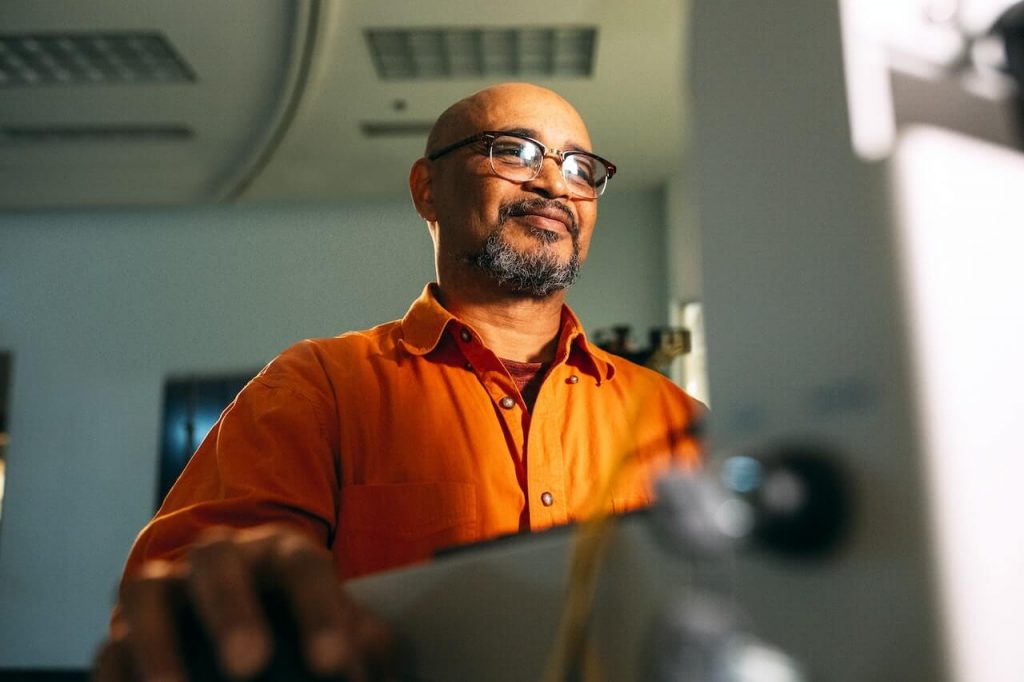
What is equipment reliability
One of the most important responsibilities in business is played by the reliability engineer, especially for companies that depend on expensive, large pieces of equipment or technology to run. A reliability engineer is in charge of monitoring equipment performance to prevent any outages that could reduce business profits. Although a reliability engineer’s duties vary from company to firm, their goals are usually the same: to reduce maintenance costs, eliminate business operations interruptions, and limit equipment downtime.
List of resources
Lowering operating and maintenance costs​
As reliability engineers, our primary responsibility is to create a strategy for tracking equipment downtime, enhancing equipment availability, minimizing production losses, and lowering maintenance costs by applying various approaches and technologies.
Managing and assessing total risk
To help a business reach its strategic objectives, we manage and access the whole risk. We are required to keep an eye on the equipment in issue, recommend when it should be fixed.
Criticality analysis
It is a tool for setting maintenance priorities and determining the most important assets. The study offers helpful data for deciding what actions will lower the risk for all plant assets.
FMEA (Failure Modes and Effect Analysis)
Failure modes are how a process can fail. Effects are how such errors can result in faults or damaging results. Analysis of Failure Mode and Effects is intended to define, prioritize and restrict these modes of failure.
Responsibilities and Duties:
Assist in ensuring the dependability and maintainability of new and modified installations.
Create and keep track of an asset maintenance plan to ensure that tactics for locating and isolating reliability issues are used effectively.
Plan actions to ensure the maintenance and dependability of resources, products, and processes.
For creating technical solutions to recurrent failures, manywe apply many methodologies strategies.
Analyze the assets, taking into account things like equipment efficacy, remaining usable life, and asset usage. The production method is utilized to complete this stage.
Use value analysis while making judgments about buying, mending, and restructuring.